Health and Safety
Heath and Safety Stand Alone Component - this is a requirement for CSCS Accreditation
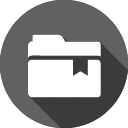
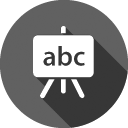
Heath and Safety Stand Alone Component - this is a requirement for CSCS Accreditation
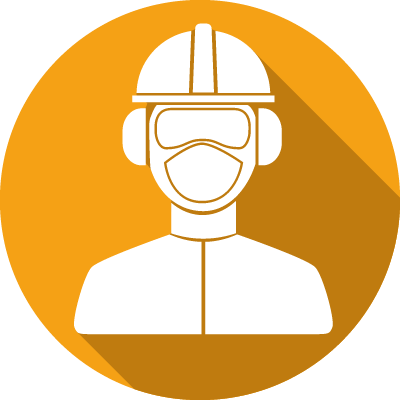
Lesson Complete:
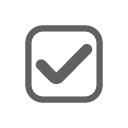
Lesson Viewed:

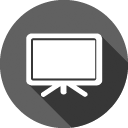
Lesson 1 - Basic Access Requirements (inc fall protection)
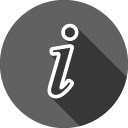
Objective
To understand the Health and Safety implications for basic access requirements to the protective coatings applicator.
- The protective coatings applicator will use different forms of access during their duties.
- The protective coatings applicator should know the basic access requirements when preparing and painting.
- The protective coatings applicator is not a scaffolder and as such should not attempt to move any access unless supervised or specifically trained.
This training unit is a basic review on access as the employer will train their employees on access and access types, depending upon the type of organisation, location of works and country of work. Specific training for working at height such as working over water etc. is not covered.
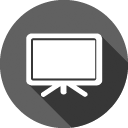
Lesson 2 - Safety in Surface Preparation
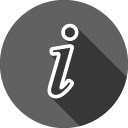
Objective
To understand the safety requirements when conducting methods of surface preparation.
- By the nature of the industry, environment and specific tasks, the protective coatings operative will be exposed to conditions that represent an actual or potential danger to themselves and others.
- The protective coatings applicator, supervisor and inspectors should be aware of the safety implications during surface preparation.
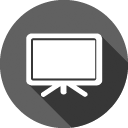
Lesson 3 - Safety in Paint Application
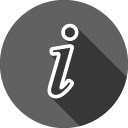
Objective
To understand the safety requirements when conducting paint application.
- By the nature of the industry, environment and job details the protective coating applicator will be exposed to conditions that represent actual or potential danger to themselves and others.
- The protective coatings applicator should be aware of the safety implications during paint application.
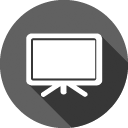
Lesson 4 - Method Statements (work Instructions)
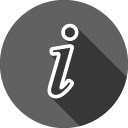
Objective
To understand why method statements are developed and who should develop them.
- Method statements should be developed for all aspects of the work.
- Method statements should be written by the supervisor or manager who will be looking after the work.
- Method statements should be clear, concise and basically detail how the work is to be conducted.
Note: Method statements are also referred to as work instructions in some parts of the globe.
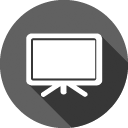
Lesson 5 - Confined Spaces
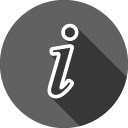
Objective
The objective of this training is to give a review of working in confined spaces.
Note: Specialized organizations conduct confined space training and should be used if personnel are to be exposed to confined spaces.
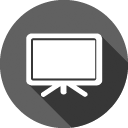
Lesson 6 - Health and Wellbeing
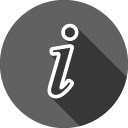
Objective
The objective of this training unit is to review the requirements for the health of the coatings applicator.
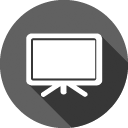
Lesson 7 - Company Induction
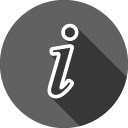
Objective
To understand the aims and objectives of the individual company, Health and Safety regulations and legislation.
- All companies must conduct an induction to new personnel.
- The company induction will vary from company to company and will differ globally.
- The company induction is a mandatory requirement.
- Additional site inductions may also be conducted for specific sites.
This unit gives guidelines on what you may expect from a company Induction.
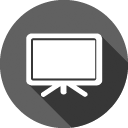
Lesson 8 - Accident Prevention
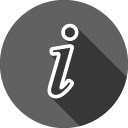
Objective
To understand that accidents can be prevented if pre-work precautions are taken.
- Evidence exists which prove accidents can be prevented.
- The protective coatings applicator, supervisor, inspector etc will be working in numerous and potentially hazardous environments.
- Never assume anything.
- Do not take things for granted.
- Be aware of the working environment at all times.
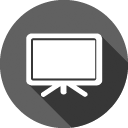
Lesson 9 - HouseKeeping
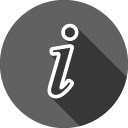
Objective
To understand the importance of housekeeping in the coating industry and general Health, Safety and Environmental implications relating to poor housekeeping.
- Housekeeping involves much more than cosmetic appearances.
- The industrial coatings industry can be a hazardous industry.
- Poor housekeeping increases the risk of hazards.
- Everybody is responsible for good housekeeping.
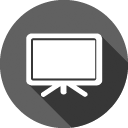
Lesson 10 - First Aid
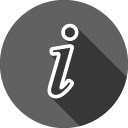
Objective
To understand that there will be an arrangement for first aid on all sites and factory facilities.
- First aid personnel should be available for all sites, offices etc. - The company has a legal obligation.
- First aid training is conducted by external organisations.
- First aid training can be given to all levels of personnel.
- First aid training saves lives.
- The number of first aid personnel will depend upon the number of people within a company or site.
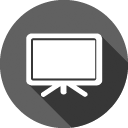
Lesson 11 - Electricity and Air Supply
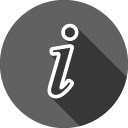
Objective
To understand the Health and Safety issues with the use of electricity and air supply.
- The protective coatings applicator and general operative will use electricity and air supply in their duties.
- Electricity and air are the most common form of power used in the protective coatings application industry.
- Electricity and air can be hazardous in untrained hands.
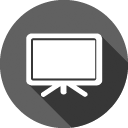
Lesson 12 - Permit to Work
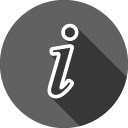
Objective
To understand that within certain tasks undertaken by the protective coatings applicator, a permit to work system may be a requirement.
- The protective coatings applicator or general operative may encounter a permit to work system during their duties.
- Permit to work systems operate in numerous working environments.
- The permit to work system is an established process.
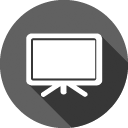
Lesson 13 - Risk Assessment (Job Safety Analysis)
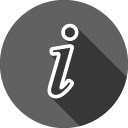
Objective
To understand the requirements of conducting both COSHH and Risk Assessments and the obligations of the employer and employees.
- COSHH = Control of Substances Hazardous to Health.
- All companies must assess the potential risks to personnel.
- No work should commence without COSHH and risk assessments.
- COSHH and risk assessments must be conducted by competent personnel.
Note: Some industries refer to Risk Analysis (Job Safety Analysis) rather than Risk Assessment.
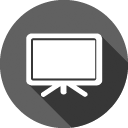
Lesson 14 - Safety Data Sheets (SDS)
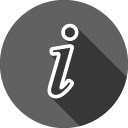
Objective
To understand the requirements for Health and Safety data sheets, referred to as safety data sheets (SDS), supplied by the coating manufacturers.
- It is a legal requirement that a safety data sheet is supplied to the buyer of the product.
- The safety data sheet should be made available at the workplace - to the operative.
- The format of the safety data sheets can vary from supplier to supplier.
- You should not use products without having the safety data sheets available.
We will also review Hazard Communications used in certain countries.
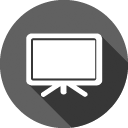
Lesson 15 - LEL, TLV, OEL, MEL and Ventilation
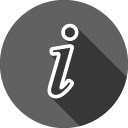
Objective: To understand the importance of the above values given in Material Safety Data Sheets (MSDS) and the need to ensure that the works are established and maintained so there is no possibility of these values being exceeded
- Material safety data sheets must be supplied with all paints, solvents, cleaners etc.
- Information on the material safety data sheets can be of a complex nature.
- The company must fully understand the requirements of the material safety data sheets.
- The product user should be aware of the technical terms and phrases.
Note the MEL and OES have been replaced by the Workplace Exposure Limits (WELS) in the UK
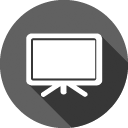
Lesson 16 - PPE (inc RPE)
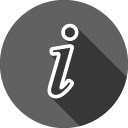
Objective
To understand the requirements for PPE. Also, understand that PPE requirements may change depending upon the type of task performed.
-
The protective coatings applicator will use PPE and RPE in their duties.
-
The protective coatings applicator should be aware of the PPE and RPE requirements on any particular task.
-
It is a legal requirement that all personnel are given the correct type of PPE and RPE.
PPE = Personal Protective Equipment.
RPE = Respiratory Protection Equipment.